The short story of assembly problems is lack of parts. Part shortages drive all kinds of waste, including: juggling the schedule; expediting; bigger lots or batches – and all of these things end up causing shortages later on in a self-reinforcing death spiral.
So how did an assembly shop which built about 10 units / day, and suffered between a dozen and 20 line-stopping part shortages a day end up eliminating all but a few (3-5) a week?
Three things, more or less at the same time. This post talks about the first:
Implement a kanban system to replace MRP ordering. They systematically studied how kanban is supposed to work, and, over a few months, put in a kanban system which I am proud to say was really pretty good. The assembly line was fed by kit carts which were picked at takt time from a small supermarket on the shop floor. The supermarket held a day or two of parts. The parts with local suppliers were replenished right from the receiving dock. Parts which had to still be purchased in larger quantities were stored in a warehouse area, and the shop floor supermarket was replenished from the warehouse daily.
The daily warehouse replenishment established the concept of isolating the problem. Their daily replenishment allowed them to set up the shop floor supermarket as if all of their suppliers were delivering daily.
All parts in the shop-floor supermarket and the warehouse were under kanban control. This means they had kanban cards physically attached to the parts (if they were separate) or the containers.
Some things they learned over time:
- The rules of kanban state that the card should be pulled and placed in the post when the first part is removed from the container. The quickly learned this was far more likely to happen if they secured the card in a place where it was in the way of either opening the container (over the folding lid, for example) or had to be moved (e.g. picked up) to get the first part out. At that point the card is in the person’s hand and he has to put it somewhere.
- The number 1 reason for lost cards was that “put it somewhere” was a pocket.
- The number 1 reason why the card ended up in a pocket was that the kanban post was more than a step away from the place where the card was pulled. That meant the person put it in the pocket “for a second” while he got the parts.
In the above case the countermeasure was simple. Put kanban collection points everywhere where parts are handled.
- The first time they tried putting a pull system in for parts ordering they hadn’t put in heijunka (production volume and mix leveling) first. That was a problem, and “problem” is an understatement.
The countermeasure was (obviously) to simultaneously implement a schedule leveling system to drive the upstream system at takt. More about that in Part 2.
- They invariably had some parts where they had more than they needed.
The countermeasure was “black cards” (though I would have preferred bright orange cards) that signified “excess inventory.” These cards allowed them to maintain kanban control of all inventory, but they did not signal replenishment.
When a card was pulled, the shop floor coordinator would scan a barcode on the card. This scan triggered an order release to the supplier, and authorized the supplier to ship the indicated quantity.
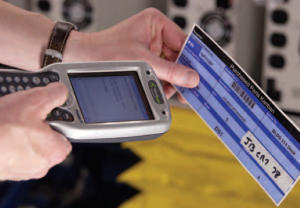
They had agreements with the suppliers that there would be an email acknowledgment of the order within 2 hours. When the card was scanned, it was placed in a slot labeled with the time when the acknowledgment was expected. When (if) that time passed and the acknowledgment had not been received, the card went to the buyer who phoned the supplier. “Did you get my order? I need the acknowledgment within 2 hours like we agreed.”
This served two purposes. First, it verified receipt of the order and eliminated a known cause of shortages. Second it “trained” the suppliers that this time the customer actually expected them to honor the agreement. They really didn’t want that call from the buyer who had better things to do.
Once the acknowledgment was received, the card went to the receiving dock. Here it was placed in a slot that indicated the day (and later on, the time window) when those parts were supposed to arrive.
Like the above case, if the time passed, the card went to our poor hapless buyer. He phoned the supplier with a simple question: “Where’s my parts?”
This reinforced that, once again, there was an expectation to honor agreements. They really didn’t care that much (at this point) what the supplier’s lead time was. Only that it was honored. The main objective when starting out was simple consistent execution.
When the parts came in, the card was retrieved, matched with the order to verify, then scanned again to trigger a receipt transaction. If there were exceptions – guess what – another phone call.
The card was then attached to the container. Since the card specified the storage location, put-away was fairly straight forward. No location lookups required.
The previous condition had been that there was no matching of receipts against expectations. Thus if parts were late, or didn’t show up at all, no one noticed until they ran out. Big problem. By trapping and surfacing problems at the two main failure points in the system, most of those problems went away after a few months.
For the purists who are reading – yes, this process has some compromises and probably is a bit obsessive on checks. Call those training wheels until there is a sense of balance. All I can say is that it worked and, in the long run, ended up to be a lot less work than chasing down and expediting shortages all day.