In a traditional kaizen event there is usually some kind of todo list for keeping track of progress implementing the ideas of the team. A common name for this form is “Kaizen Newspaper.” The below example is pretty typical. This is a real one from the early 2000’s.
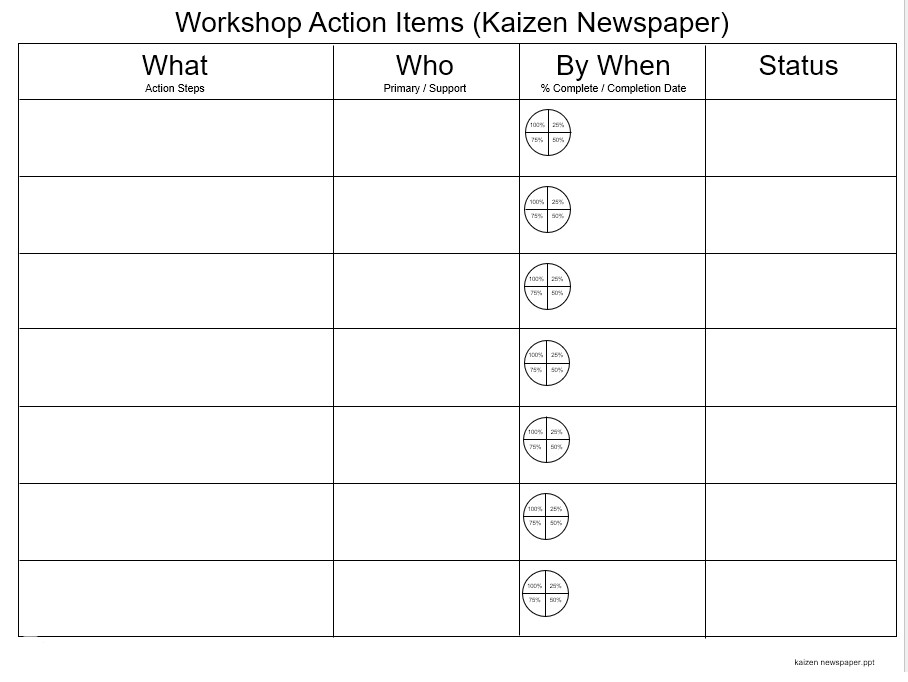
This form reflects a bias in western (certainly USA) business to focus on getting stuff done. I think it might be helpful to reflect a bit on the assumptions that are built in to this structure.
One of my favorite quotes is from Grace Ng: “All customers have problems, all problems have solutions. But not all solutions have problems, and not all problems have customers.”
In the context of this form, the “What” or “Action Step” is usually a solution. We are going to do something. And once the “What” is decided, then the rest falls into place- Who is going to do it, by when are they going to get it done, and what is the current status? And it is all to easy to get pulled into the implement vortex without ever thinking about “Why?” are we doing this – what are we trying to accomplish? How will we know we have accomplished it?
This is also a typical structure for a management staff meeting, and even discussions about strategy – they devolve into “What are we going to do?” and often skip over “Why are we doing it?” In other words, “What problem are you actually trying to solve?”
The “Progress Wheel” tracking percent complete implies an assumption that there are multiple steps involved, and implies a conversation about what those steps are as that wheel is filled in. The quality of that conversation depends on the skill of the coaching and facilitation.
The “By When” or “Due Date” implies that days will pass before we expect this action to be completed. It might be tomorrow, but often is not in practice.
This means that we expect that we wouldn’t get everything done that week. These newspaper items frequently carry over and are supposed to get done as follow-up work after the kaizen week is over. In practice, these things often fall victim to the daily whirlwind and languish. The “newspaper” is now more of an archive. It isn’t about today anymore.
Here is form from another company in the same era. As an aside, this company added “Complexity” to their list of wastes, and perhaps we can see some of that reflected here. But it takes a step in the right direction by adding “Problem to be solved” and, through the “Target Reference” block tries to tie it back to an intended result. It also has a column for “Results” on the far right.
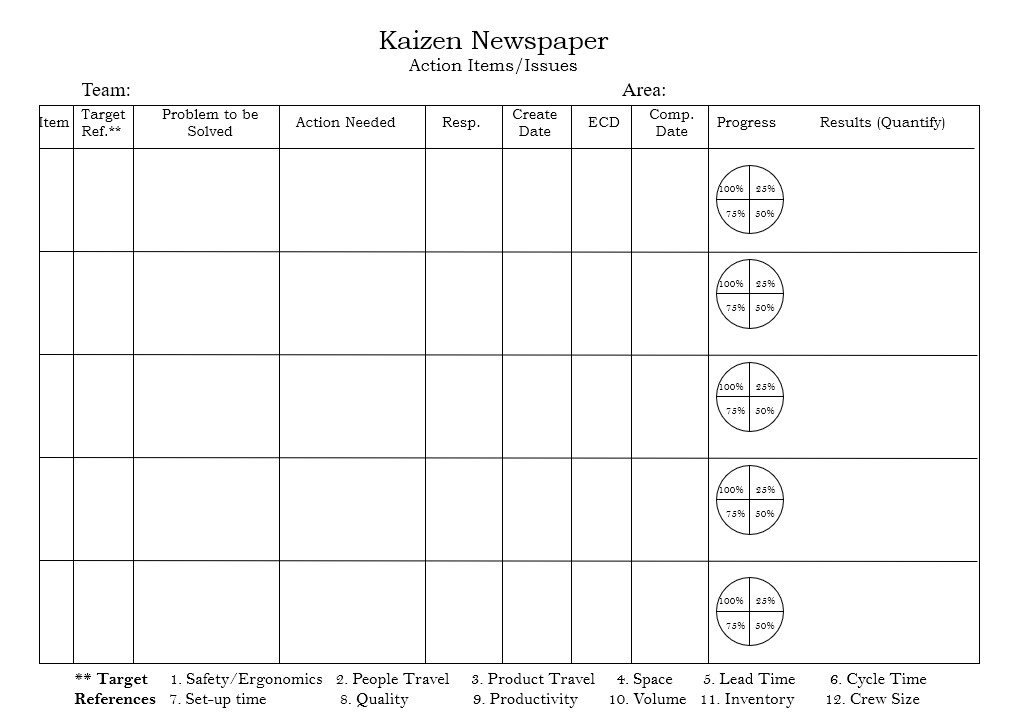
What neither of these forms does, though, is ask “What result do we expect? They depend on skilled facilitation and coaching to ask that question as the team is proposing the idea. One of the challenges we often face (again, in the West and especially the USA) is with our focus on action we don’t default to asking that question.
One exception I experienced in May 2001 was a Shingijutsu consultant (and I don’t remember who it was, unfortunately) who had us modify our kaizen newspaper that week to add a column that captured the cycle time we expected to save as a result of implementing that step. (I know the date because I did the modification on the original file and still have it in my archives.)
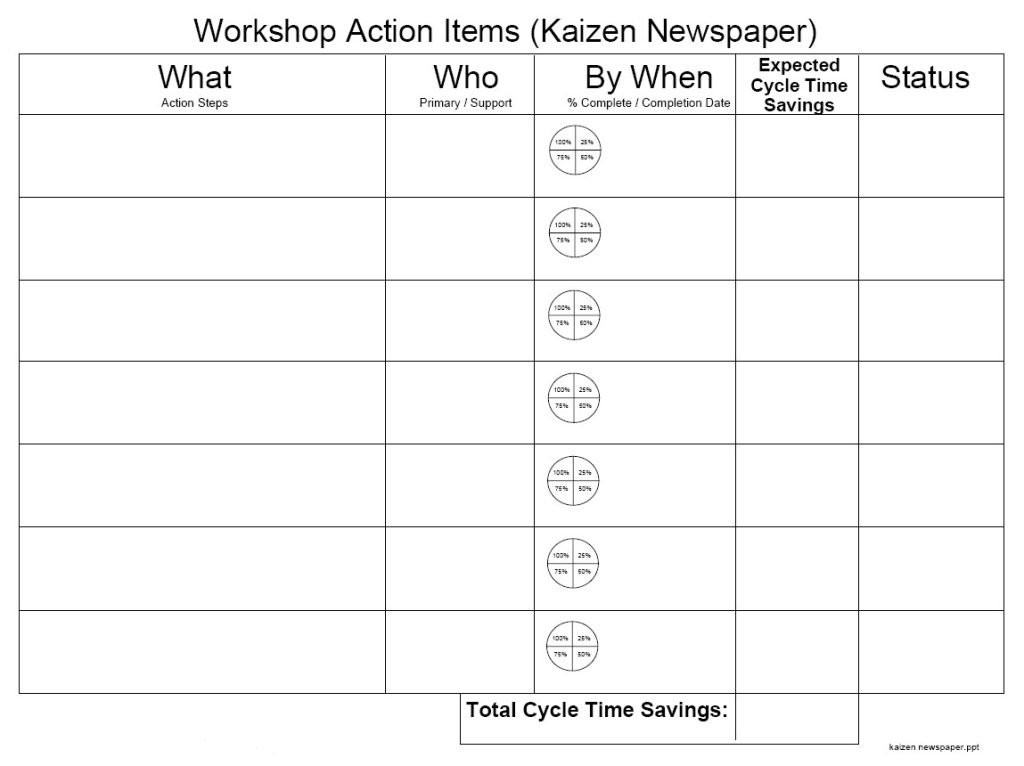
The idea was to make sure that we were implementing enough changes to deliver the cycle time target.
What it didn’t do, though, was capture the actual cycle time savings from the action.
What Are We Trying to Achieve?
A common assumption in many continuous improvement efforts is that if people participate in enough of these kaizen events they will experience a mindset shift. The challenge here is that the events themselves are usually focused more on results than on explicitly teaching and practicing the mindset1.
Don’t get me wrong – results are important, especially if you want to keep doing this. It is rare that any organization has infinite (or any!) patience for a lot of discussions around history, hypotheticals, or theory.
That means we have to actually solve real problems. We have to get stuff done. We have to at least look like there is a bias toward action if we want to survive as change agents in most organizations. The key is to solve the problems in ways that develop people’s problem solving skills.
That means making the mindset we want to teach more explicit.
This is the whole point of Toyota Kata.
Build the Coaching Into the Process
A highly skilled coach or facilitator brings teaching the problem solving / scientific mindset into the process, regardless of the forms and structure being used. But we can make this easier on both the coaches and the learners with adjustments to the structure.
While all of the artifacts of Toyota Kata are designed to do this, I want to avoid my tendency for scope creep and stay focused on one (really two) of them that fulfill the intended purpose of the Kaizen Newspaper in a way that develops peoples problem solving skills.
The Learning Record (aka the Experiment Record aka the PDCA Cycles Record aka the PDSA Cycles Record)
I call this form the “powered gear” that drives the entire process. Let’s look at the structure2. The form is structured in a way that turns action items into hypothesis tests.
The first, obvious, thing is that we aren’t just saying what we are going to do and by when. Each action, which we are calling a Step or an Experiment, has a specific predicted result or outcome. Separating the step being taken (the action) from the intended or predicted result helps people distinguish between the two. Allow me to elaborate.
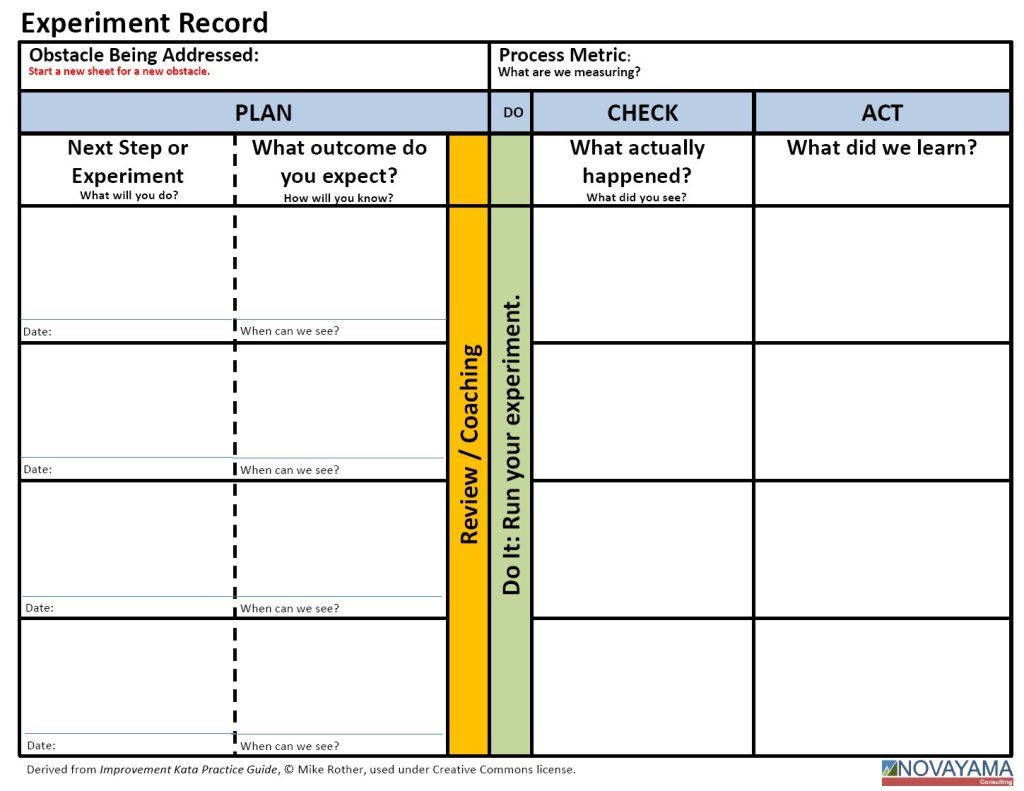
I often see a result or outcome being listed as something that we are going to do. This can go as far as something like “Increase gross margin by 3%” as an action to take.
But that is an outcome (and an indirect outcome at that). It doesn’t say what we are actually going to do that we predict will produce that outcome.
One (the action) is cause. The other (the result) is the effect. Distinguishing between cause and effect is one of the core fundamentals we are trying to teach people who are making improvements or changes.
Explicitly separating what we are going to do from the result we expect helps people practice this mode of thinking. But the coach has to be prepared to ask good questions rather than just buying whatever is written in the boxes.
Taking this a step further, I have sometimes found it helpful to ask a learner to first decide what they want to learn, or the effect they are trying to achieve and write that in Box #2 first. THEN I ask, “What action are you going to take that you think will [ read what is in Box 2 ] ?” and write that action in Box #1.
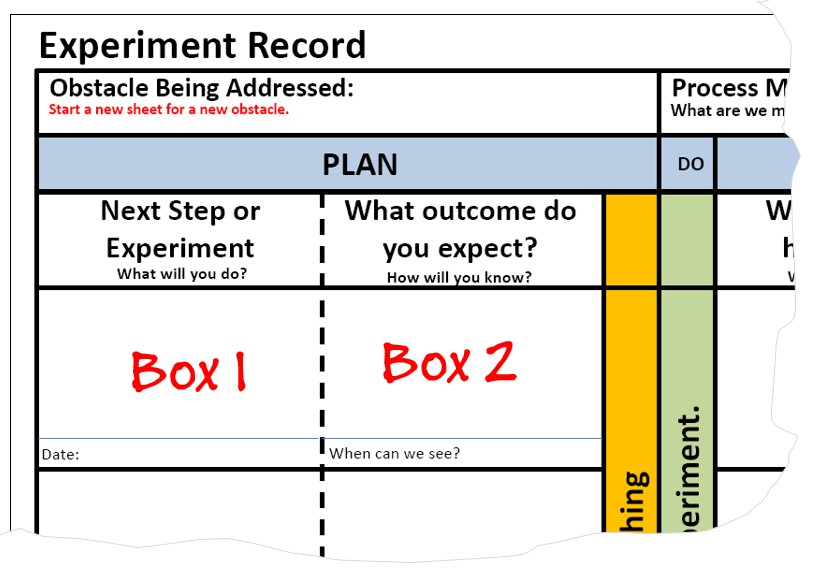
I can also ask the learner to say, “I intend to [ read what is in Box #1 ] in order to [ read what is in Box #2].” For example, “I intend to rearrange the end of Alice’s work path in order to cut 3 seconds of walking from her cycle time.” If that sentence doesn’t make grammatical or logical sense, there is more thinking to do.
In general (this is a rule of thumb, not a hard rule) there are three kinds of actions that get listed here.
- A straight up hypothesis test – make a change with a predicted effect on the process, like the example with Alice’s work cycle above.
- Gathering more information – for example getting more detailed information about the current state of part of the process. This might be something like breaking down the cycle time of an individual operator into discrete steps. This could be where I learned Alice has 4 seconds of walking back to the start.
- Trying something in order to learn. For example, we have a target process that we can run, but we don’t have a good idea what the obstacles might be. The experiment would be something like “Run to the target process and carefully observe what actually happens” and the expected outcome would be “To learn what the obstacles are.” This is particularly effective for finding sources of process variation.
In general, and this is also more of a guideline, I want to see enough detail that we could give the sheet to someone familiar with the process and they could carry out the experiment from what was written. (This is just a thought experiment! DON’T actually do this. I can confidently predict that you’ll end up repeating the experiment because “what actually happened” won’t be what you thought – though that is an experiment in communication in its own right.)
The “Review / Coaching” line (yellow on this form) is the gate. We don’t cross that line until we have the coaching conversation, just to make sure everything I mentioned above is tight.
All we have at this point, of course, is a hypothesis. “If I do what is written in Box #1, I predict I will see (or learn) what is in Box #2.” Now we have to test that hypothesis. That is why we call this an experiment.
WAIT A MINUTE! Back up! What Obstacle Are You Addressing?
When you are running experiments, you are working to overcome some obstacle that is between you and your goal – your target condition. You want the process to operate in a new way (the target condition), but for [reasons] it can’t. Those reasons are obstacles.
This is different than the typical approach of just brainstorming a bunch of things to do and implementing them. We are targeting a specific way of operating (which is often an intermediate stage on the way to something more challenging).
We want our learner / improver to have an obstacle, problem, unknown of some kind, in mind. It may take – it usually takes – more than one experiment to learn enough to overcome that obstacle and move on to the next.
Address one obstacle at a time.
The Experimenting Record provides structure to reinforce this mindset by having the improver write the specific obstacle or problem in the space on the upper left corner before engaging any experiments. If they don’t know what the obstacles are, then write that as the obstacle, try to run to the new work pattern in order to learn.
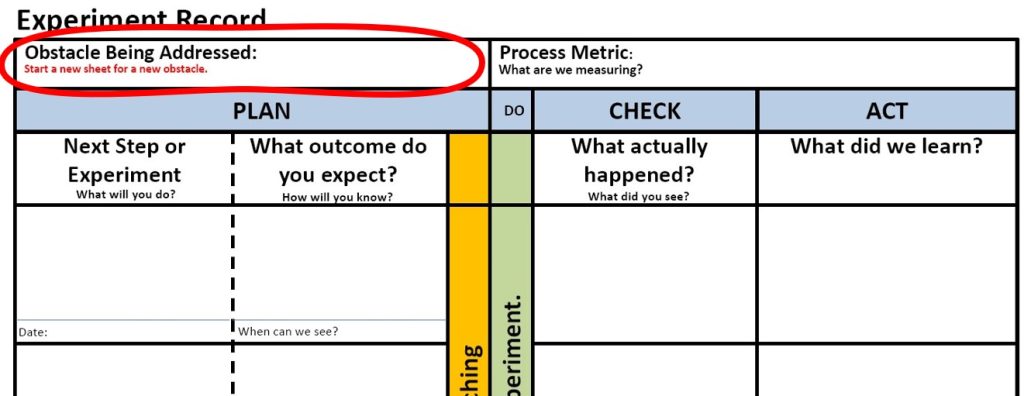
“What problem are we actually trying to solve?” is a question that can often reign in an otherwise chaotic discussion about what to do.
The upper right corner has a space for a “process metric.” Without going off on another deep tangent, this is the attribute of the process result that we are trying to affect. The target condition should include a target value for the process metric so we can tell if we are actually making progress toward the target condition.
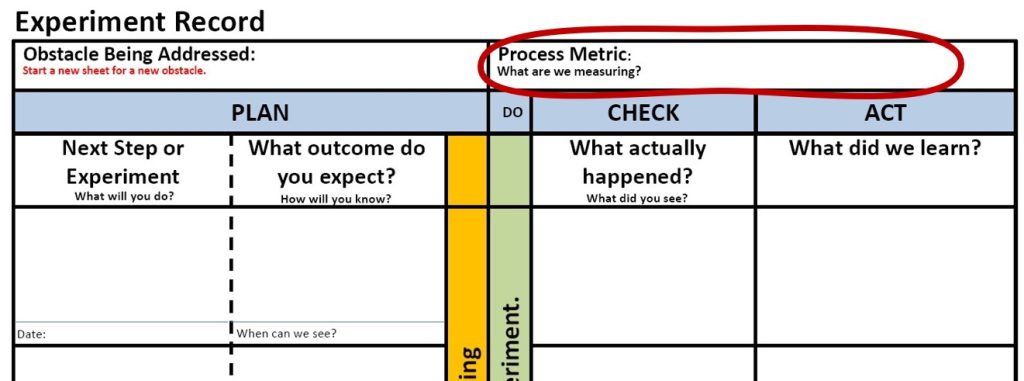
The process metric can be something like the cycle time of a particular operator; the minutes of exercise I am trying to achieve every day; the amount of variation in a process parameter we are trying to control. These are all things that we can immediately, directly, measurably affect by changing the process in some way.
Why did I address this part of the form second when it should be done first? Because it is very common to bleep over this part and just start writing experiments only to have the effort get diffused later.
Maybe my little digression was unexpected which might result in you remembering it a little better.
Now – Run Your Experiment
In the classic Plan-Do-Check-Act cycle we discuss “Do” and “Check” as sequential activities. In practice they are simultaneous, or nearly so. You should verify that the action you are taking is actually the action you planned to take. CHECK that your DO matches your PLAN.
If you ended up doing something different, you want to make a note of that, because you likely can’t say your plan didn’t work if you didn’t actually carry it out. What ACTUALLY happened? What did you experience? What did you see? What result did you actually get?
The things that we want to see written in Block #3 of the Experiment Record are objective facts. Please don’t just repeat what was in Block #1 in past tense. As a coach I want to see what you actually did as well as the actual outcome vs the planned outcome. And this includes outcomes that you didn’t anticipate. Sometimes those are good surprises – collateral benefit. Sometimes you learn that you need to pivot to a different idea.
Block #4 is subjective. What did you actually learn? There is usually more to this than what was simply in Block #2. This is also a good time to look at your obstacle list and make additions, deletions, and edits. Those are also things that you learned.
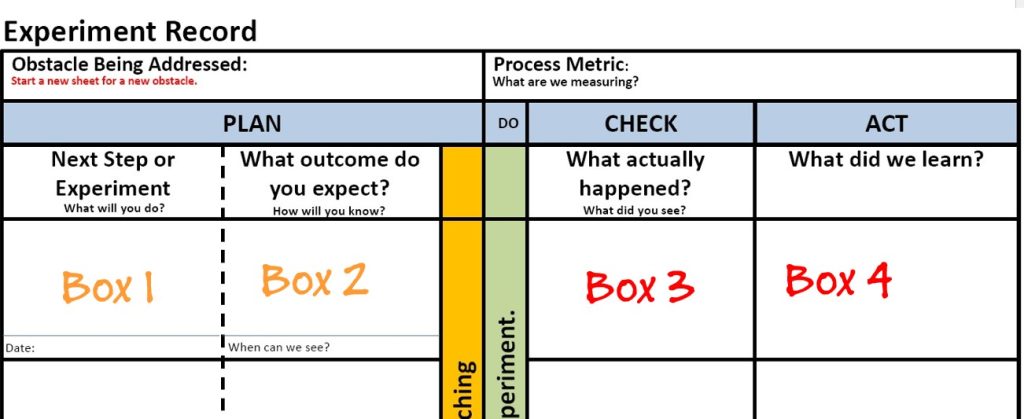
After Your Experiment
If you have had an impact on the current condition, update that. As I mentioned above, scrub your obstacle list and make sure it is up to date.
Have you achieved your target condition? If yes, awesome. Time to do a summary reflection, take a deeper look at your current condition, and establish a new target condition with new obstacles. (Same thing if you have reached the “achieve by date” without hitting the target condition.)3
If not, are you still addressing the same obstacle? If yes, then move to the next line on the experimenting record and fill in Block #1 and Block #2 for your next experiment.
In all cases, let what you have learned inform your next step. Notice how this is different than blindly executing a complex action item.
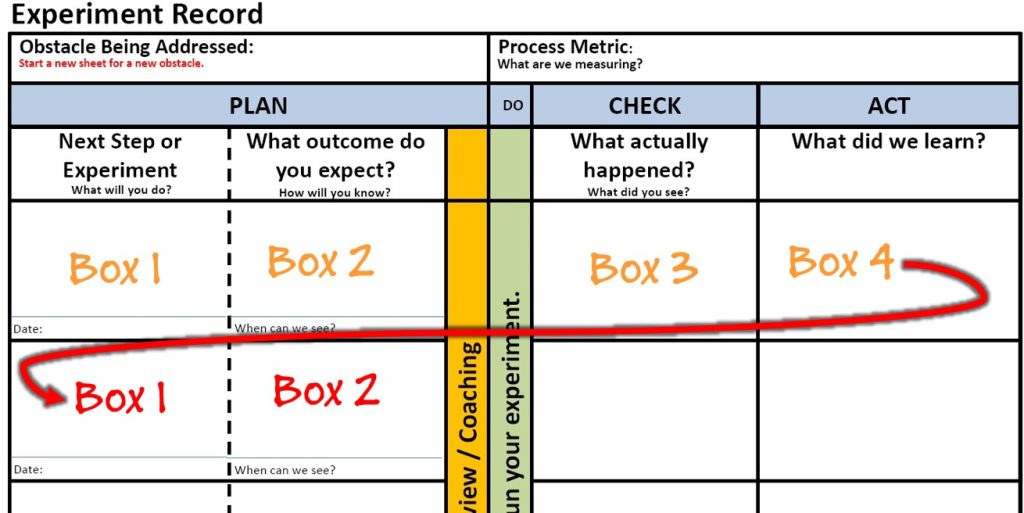
If you are addressing a new or different obstacle, then same thing, but please start a new form.
Why So Much Detail?
Our results-as-action-item corporate culture has a heavy bias to glossing over the details, and they are often not discussed or thought through. An action item might have a due date that is weeks in the future, and other than saying “It’s on track” not much will be discussed.
The Experiment Record is designed to have a small step every day (or nearly every day), discuss what was learned, and allow that to inform the next step so we aren’t blindly executing into something that has become irrelevant.
To be clear, a skilled, experienced coach can bring all of these questions out with a team using the traditional kaizen newspaper. The purpose of the Experiment Record is to make it easier for everyone, the coach included, to dig deeper into the kind of thinking we are trying to teach. It makes these questions explicit rather than relying on the experience and skill of the coach or facilitator.
Honestly, having these things explicit also establishes an expectation that the coach is going to ask about them. When a coach or facilitator starts pushing for more detail within the structure of a process that is overtly superficial they can, well, come across as a jerk. We call it “Socratic Teaching” but we have to remember what happened to Socrates. Better to have a process that makes the structure transparent to everyone.
Even outside of the Toyota Kata ecosystem, this process can bring a cadence of accountability to things as mundane as staff or project status meetings. The key is to not allow any step to go beyond the next scheduled meeting. “I can have that done in four weeks” becomes “What will we do before next Wednesday?” and “What result do we anticipate from taking that step?”
Back to the Kaizen Event
Try this experiment in your next kaizen event.
Throw away your kaizen newspaper.
Ask your team to list the problems that have to be overcome to achieve the goal for the week (which is really a target condition). Put those on a seperate sheet. You can use the Toyota Kata “Obstacle Parking Lot” but that is really just jargon. Call the problems whatever you want – just make sure they are problems and NOT actions to take, or things to implement. What is it about the process that makes it hard to change to the new way? What kind of issues come up that prevent the new way from working smoothly?
Then pick off one of those problems and start a rapid cadence of learning using the Experiment Record format. Keep those cycles quick. Can you do one every 15 or 20 minutes? Probably. The first experiment may well just be a simulation of sorts to learn if this idea is even worth pursuing. Cardboard, tape, holding things by hand to represent a fixture.
If you have a large team you might be tempted to work on more than one of these problems at a time. OK – but first convince me there won’t be any cross-talk between those problems or those experiments. It is really hard to learn when the conditions are changing under your feet because someone else is tugging on the other end of the rope.
At each major step you want to work to stabilize what you have before making the next change. Do this quickly, but incrementally. Doing otherwise is leaving a shaky process behind, and this is disrespectful to the people who have to deal with the aftermath.
At the end of the event celebrate, not so much the results, but what you have learned about making improvements. Wherever you are is where you should be.
Come Monday morning – here is the cool part – don’t stop. Maybe you only run one experiment a day vs. three or four every hour, but keep moving. Keep those coaching cycles running at least once a day.
Congratulations – you are now solving problems in a way that develops people’s problem solving skills.
What’s Next?
Did you find this helpful? Would you like me to go into similar depth on other pieces of the Improvement Kata, such as obstacles, process vs. outcome metrics, etc? Is there something specific you would like me to cover?
Leave a comment and let me know.
1 Another challenge is that most leaders only participate in these events a couple of times a year. The question, then, is what do they practice the other 48 weeks?
2 There are a lot of variations of this form, but those variations tend to be limited to phraseology. The fundamental structure remains the same.
3In a week long kaizen event you should really only have a single target condition to reach by the end of the week – if it is planned well – another deep digression I could go into.