In early spring of 1999 I was sitting in a classroom at Boeing with a couple of dozen other employees. Everyone with a “management” job code was being sent to this session over a few weeks’ time.
The topic was a major new direction for the company. From this point forward, management was to use “shareholder value” as the primary consideration for decisions.
The main emphasis here was on a financial metric that would drive all decisions: RONA, or Return On Net Assets.
This was obviously a long time ago, and I have long since (unfortunately) discarded the handout materials because I wanted to reuse the fancy tabbed folder for something else. But as I recall, there were two primary topics discussed.
The first one was around what “shareholder value” meant. To that end they explained why maintaining a high stock price was important to the company: So they can raise money more easily for growth.
This was all about stock price. They didn’t talk about profits or dividends. Nor did they talk about executive bonuses or using excess cash for stock buybacks to raise the price of outstanding stock rather than investing that money into developing new aircraft; improving existing products or processes; or distributing that profit as dividends to the shareholders.
Of course, a high stock price enriches those people who already own shares, and makes options and stock grants more valuable, but they didn’t get into that either.
With the justification aside, they next had us go through exercises calculating net present value and ROI for a hypothetical capital investment in tooling – as though a shop floor supervisor would do this at any point in the course of their job. Maybe they wanted to show the thinking behind how requests for things like upgraded tooling were evaluated. I left the class not really sure of why they took us through that. I already understood those calculations from my background, but the shop floor guys were kind of scratching their heads.
The second part of the class involved a facilitator leading our group through discussion of the “grieving process” as it relates to “change” and trying to draw out how we felt about it. Then we were video-linked to other groups in identical sessions, perhaps in some effort to show how we were all in this together. Again, I wasn’t sure of the point of all of this.
Sidebar: If anyone reading this has better memory or still has any of the original materials from that class, I’d love to talk to you.
Overall, this shift was about the management process becoming financially centric. Boeing’s performance as a company since this shift has been (painfully) obvious to anyone who has been following business news over the last decade or so. The details have been covered elsewhere, so there is no need for me to reiterate them here. However, if you are interested in a succinct and well researched history, Petter Hörnfeldt is doing a fantastic job with a multi-part series on his Mentour Now YouTube channel.
Optimizing for RONA
RONA is calculated by dividing net profit by total assets. The obvious way to improve RONA is to improve operations and optimize processes to create maximum customer value for any given level of capital investment.
And this is exactly what Boeing had been working to do prior to this pivot toward “running like a business.” It was even developing a name: “Working Together.”
The Original Pivot: From “Do What You’re Told” toward “Working Together”
Ten years before this shift toward financialism, Boeing had been going through a different shift.
The Boeing that emerged from the early 1970s downturn was highly engineering centric. Engineers ran the company, engineers decided what would be designed and built. In the world of production, though, the culture was far from ideal.
I hired into Boeing in July of 1989. I was fresh out of the Army, and one of the contractors I had worked with in my last assignment was working as an Industrial Engineer in Boeing Flight Test. He introduced me, I had an interview (and couldn’t get a word in edgewise), and was offered the job.
At the time, Boeing was scrambling to keep up with deliveries for the hot-selling 747-400, and the Flight Test teams were helping prepare new planes for delivery. This involved inspections by the customer and test flights which, in turn, produced lists of things that needed to get fixed. My job, essentially, was to keep track of what was getting fixed, by who, and when, and produce daily reports on progress. My first plane was RT001 (internal production line number), the first 747-400 Combi being delivered to KLM.
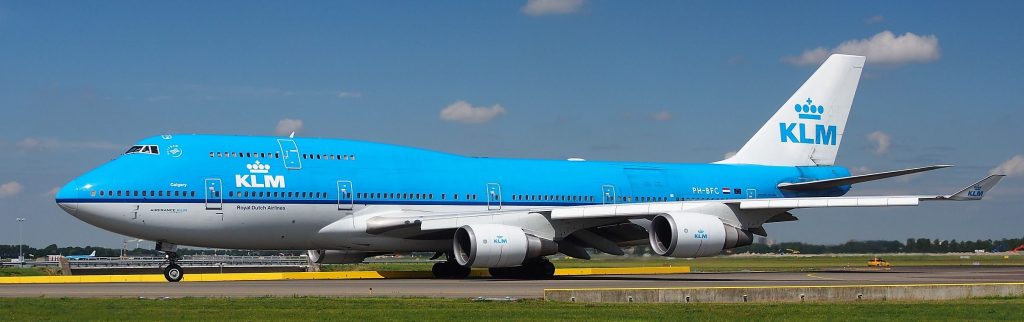
The production processes were archaic, with legacies going back to the 1940s. Industrial engineers dutifully analyzed each job, and determined the time it should take. They used those times to build what were essentially Gantt Charts of the production plan for each worker. These were called “bar charts” and “making your bar” was, for all intents and purposes, how workers were evaluated.
The system was not robust, overtime would swing: When production managers were being beaten up about being behind schedule, they would turn on the overtime. A few weeks later, when overtime costs were climbing they were beaten up over that, and overtime would be shut down, leading everything started to get behind again.
Those costs were out of control. One bit of “common knowledge” in the company at the time – and I have no way to know if it was true, but it is certainly credible to me – was that for every four 747-400’s that Boeing delivered, they built the equivalent of five and threw one away into the scrap bins.
There wasn’t a lot of focus on the things that actually got in the way of people doing the work. There wasn’t time for that. Things were behind, and there was work to do.
With all of that, though, things had started to change. Boeing had brought in some of the well known quality names (Conway, Deming) in the late 1980s. In the late 1980s and early 1990s Colin Fox, an early consultant in the world of flow production, had led a series of study missions to Japan that engaged Boeing’s top 100 or so leaders.
Some of the pull quotes from those sessions were interesting – like the indignant reaction that Airbus would somehow dare to talk to long-established Boeing customers. These study missions were quite eye-opening for the participants.
These leaders had learned about the emphasis on quality, consistent execution, focus on the needs of the customer, using flow and just-in-time production to progressively surface problems, and engaging everyone to progressively drive those problems out of the system.
Those groups came back from their experience with an visceral understanding that the status-quo wasn’t going to cut it in the face of the then newly emerging Airbus. They realized then that Boeing had to transform itself from an engineering company focused solely on meeting engineering challenges to one focused on meeting the needs of the customers. But the key to meeting the needs of the customers was more than just understanding those needs better. It required creating a company culture that supported employees – everyone – to do the right thing for those customers.
Soon after these study missions someone decided, “Everyone in management needs to hear this.” The result was a 32 hour course that ran two days, then a break, then two days the following week. During the break, work teams were expected to do some homework assignments.
The idea was that the original leadership teams would teach this course to the next level of leadership, then train people at that level to teach the next – and cascade the teaching through the leadership ranks. The hypothesis was that since the message was coming from your immediate supervisory level, the thinking went, it would resonate better than if it was just professional instructors.
Sometime in late 1992 somebody then decided, “EVERYONE needs to hear this,” and the deployment was changed to include everyone in the company, all 130,000 people. That was, in my opinion, a smart move if only because it was a move toward transparency. The class wasn’t some secret management thing.
I was aware of all of this because one of the supervisors (though not my direct supervisor) in the Industrial Engineering group I was working in had become an evangelist, and ultimately put in charge of coordinating the delivery of the class through about half of the company. (The “Renton Division” – at the time Boeing was essentially North Boeing (in Everett) and South Boeing (in Renton.))
He and I had a lot of common values and background, and he shared a lot of his excitement with me.
When they started rolling the class out to second shift he told me they had an extra slot on one of the sessions and I managed to wrangle attending, probably about a year before I would have otherwise. I went to a 2nd shift schedule, and attended the class… on crutches, as I was recovering from ACL reconstruction surgery at the time. This would have been late spring 1993.
But his real agenda here – I later learned – was that he wanted me to teach it. To that end, he had established a program of inviting “non-management volunteers” as instructors. Within a month of having attended the course, I was one of the instructors delivering it. I taught it (always as part of a team of four) about a dozen times, always to an audience of hourly employees (union members). They could be a tough audience, but not necessarily for the reasons you might expect.
Why am I telling you all of this?
I think it is important to relate that this is my personal story and experience rather than just reporting on something. I do not pretend to be a journalist, and am certainly not objective in this case. While Boeing had lots of issues, at the time I felt they were generally trying to move in the right direction and the potential was, simply put, unlimited. I believed, and still believe, that Boeing at the time had the technical capability – if they had the financial resources – to land people on the Moon (and return them safely to the Earth).
Managing for World Class Competitiveness
The name of this course was Managing for World Class Competitiveness.
The core message was (quoting from an introductory slide):
- Management is responsible for and committed to making Boeing a world-class company.
- To become a world-class company requires an understanding how world-class companies operate.
- Continuous Quality Improvement encompasses all of what you are about to learn.
Remember that this was 1992 or so. The “continuous improvement world” was in a gradual shift from the language of TQM (big ‘Q’ Quality) to looking at the Toyota Production System as a specific benchmark. Although The Machine That Changed The World had just been published, the word “lean” was not yet in common use to describe these things. We referred to “Japanese Management” or “JIT” to describe what, today, we call “lean.”
Other context – Six Sigma was largely a Motorola thing, and was just beginning the morph that happened as it passed through G.E. It for sure had not yet had the word “Lean” spliced onto it. I think that happened in the late 90s, and if I recall correctly (and I could be wrong), it happened at Maytag.
Other WCC Key Messages (Quotes from Key Slides)
- Superb manufacturing processes, delivering world-class levels of quality, are a primary source of competitive advantage.
- The product development process, likewise, must be focused, fast, and integrated with production.
- Leadership and management systems focus on operational strategic objectives that, in turn deliver financial performance.
This last bullet is a critical point. It is the one that was totally lost later.
World Class Principles
Without going into all of the content, I think I can summarize the core messages with the “Twelve World-Class Principles” which, I think, have aged pretty well:
- Quality First: policy in action.
- Customer-driven.
- Partnership with people.
- Management leadership.
- Quality built in.
- Organizational alignment.
- Cross-organizational coordination for the customer.
- Elimination of waste: Focus on adding value.
- Reliable processes through reliable methods.
- Healthy work environment.
- Simplify.
- Continuous improvement as a way of life.
The Impact
The course rolled down through the company into 1994. There was also an economic downturn happening, at least in aerospace. Some of the hourly mechanics in the classes I was teaching had already been notified they were being laid off. That could have created some real awkward moments – and it did. But most of those guys were actually thankful to have been sent to the class when there was no business need to do so. “You guys are showing me how to run a business if I end up starting one.”
In the background, also in the early 90s, Boeing was beginning to experiment with things like 5S and “Accelerated Improvement Workshops” (AIW) (aka kaizen events). Most of these were small-scale tactical affairs.
Also happening in this time was the development of the Boeing 777. Alan Mulally, as the chief engineer / program owner (and later the President of Boeing Commercial Airplanes) had introduced the theme “Working Together” to describe how they were going to involve key customers, like flight-line mechanics from United Airlines, directly into the process of specification, design, and testing.
The new plane was also being designed with producibility in mind. The structural designs were far more tolerant of production variation, for example. This was also the first Boeing plane to be designed in electronic 3D CAD systems that showed things like interference. Boeing had worked with Dassault Systems to develop CATIA pretty much for this project.
Outside of 777 development, around 1994 or so, Pratt and Whitney (who are profiled in Womack and Jones’ book Lean Thinking) introduced Boeing to Shingijutsu, the Japanese consultants that were made famous by that book. My experience was that they, especially Mr. Iwata and Mr. Nakao, challenged Boeing to take the game up quite a few levels.
Peak Boeing
On April 9, 1994 I took my then-girlfriend-now-wife as my guest to the rollout for the new Boeing 777. There were actually 15 “rollouts” that day – this was a major celebration, and over 100,000 people attended. The company had hired Dick Clark Production to stage the event, and even thinking about it today still brings (good) chills. It was a triumph moment for everyone.

What followed was regarded as the most intense, and smoothest, flight test and certification program Boeing had ever done. The goal was to deliver this long-range twin-engine plane with the certification to fly long-haul over water from day one. This was the first time that had ever been done. It was ambitious, to say the least, as these were also new engine designs from G.E., Pratt and Whitney, and Rolls Royce. Side note: The engines on the 777 are roughly the same outside diameter as a single-aisle airliner’s fuselage.
The first 777 delivery took place in May, 1995 – pretty much exactly as had been promised back in late 1989/early 1990 when the design program was officially launched.
All of the above was a triumph in the engineering and product development process.
Production, though, still had work to do.
Working Together in Manufacturing
The story about the overtime cycles I told earlier was the world my by-now-wife was dealing in when she was working night shift on the 777 assembly line in 1998 as she was part of the team putting together the fuselage section that sits over the wing (called the “44 Section”). By the time she was working there, they were running a takt time of 3 days, which, for something this large and complex, is impressive.
While the design of the airplane made the airframe much easier to assemble compared, for example, to the 1970 era 747, there were still supplier quality issues and general “stuff” to deal with in production. They worked very hard, much harder than they really should have needed to.
While this was all happening in Everett, there was a revolution happening in Renton.
At some point, Mr. Iwata, the chairman of Shingijutsu Consulting, had challenged Boeing to build planes on a moving assembly line.
The original response to that challenge was a team trying to design a moving assembly line. Their approach was to try to work out solutions to all of the problems that would entail and then build the line and run it. There were a few iterations of this effort, but they all got overwhelmed in the thousands (millions?) of details. They were trying to develop solutions to every problem they could imagine.
Just for context, this is what Boeing 737 final assembly looked like in 1990 when they were running a cycle of 20 planes / month (one per workday):
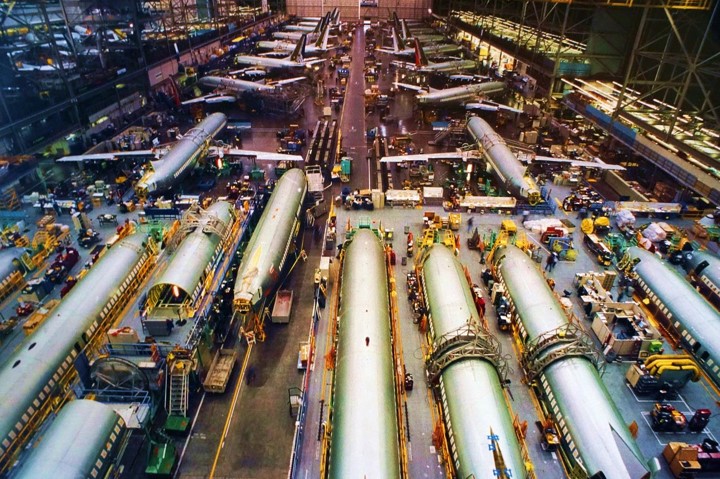
There were actually two lines running parallel, each one on a two day cycle. Toward the top of the picture you can see the “slant positions.” Each time the line was indexed, it generally took a shift to, in succession, pull each plane back, then forward, then dock it into the next position. And because this was a schedule-driven line, the planes moved on time, ready or not. Incomplete work became “travelers” – jobs that traveled with the plane to be completed later when, for example, the parts became available. Exactly who was supposed to do that out-of-sequence work while everyone was busy with the scheduled jobs was a little vague. Usually… overtime.
There are about 23 planes of work-in-process in this photo.
The assembly manager for 737 then ran an experiment. Instead of trying to solve all of the problems they could think of before trying anything she took the opposite approach. She got an RV winch, bolted it to the floor by the door, hooked the cable to the last plane, and started pulling it – slowly – through the work position. If everything was going smoothly, they kept pulling. If something disrupted the work, they stopped the winch, wrote that down, and picked off a few of those things to try to fix on the next cycle.
It took a few years, but this is what the same line, making the same planes, at the same one-plane-a-day rate, looked like by 2000:
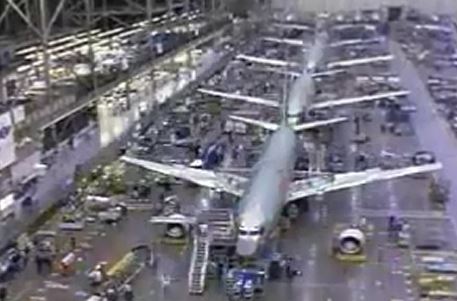
There is only one line. The planes are nose-to-tail. What you can’t see here is that those planes are all moving toward the door at about three inches per minute.
After I had left Boeing, I had the opportunity to organize a study mission group through a series of factories in the Puget Sound area. One of them was the Boeing 737 moving line. This was late 2002, they had gone through a recession, and were in the process of ramping back up. (There was no public tour for this, you had to know someone.)
This is part of the report I submitted to our VP of Operations at Genie (Colin Fox – remember that name from earlier?) the next day:
Renton is building the 737 at a rate of 14 planes per month with a two shift operation on a moving assembly line. Although they are very clear that they are still in transition, our tour guide (the 737 program manager) told us their hours worked per plane have been cut roughly in half. The reduction has been through the elimination of rework and overtime – building the plane on the intended schedule – rather than absolute gains in productivity. They achieved this by implementing aggressive expectations for problem escalation and response from support organizations. This has been a major culture shift as the support organizations shift their approach from “I’ll get back to you” to a sense of urgency about getting production started again. There are andon and status screens for each position on the assembly line.
Additionally they have ship sets (What we would call a “unit set.”) of parts and tools delivered to the work position for each shift of work. This has eliminated the shift start-up ritual of a mechanic looking up his jobs, investigating the engineering drawings, going and finding his parts, going and getting his tools, visiting the chemical crib to get his materials, etc, etc. Instead the mechanic can get straight to work.
Just as impressive is that they do this with less than half the number of aircraft-in-process as they would have had with their traditional slant-position approach. Where they used to have a month or more of flow through the line they are down to a little over a week.
Mary, our tour guide, also discussed some of the leadership challenges at length. She encountered considerable “what about” type resistance from traditionally thinking support organizations who wanted to solve every problem they could imagine before proceeding. She was adamant that the only way they could get anywhere was to just try it and see what happens. They started the way Henry Ford did – by pulling a plane down the line with a winch to see what disrupted the flow, and fixed the problems as they came up.
Boeing’s other assembly lines are studying the lessons from 737 (and 717 in Long Beach). The gains realized in converting from a pulse type line to a continuously moving line are no longer in question there because someone has gone and tried it. Equally impressive is that the “Snohomish Airplane Company” (Everett) is studying and adapting ideas from the “Lake Washington Airplane Company” (Renton). Traditionally there has been very little travel of ideas across this divisional boundary. (“Big airplanes are different from little airplanes” and vice-versa.) The 747 is continuously moving through part of its production – using the winch mechanism that 737 gave them.
On that same tour we also saw amazing efforts in their Fabrication Division in Auburn.
Like all of Boeing’s operations, the Fabrication Division has been severely impacted by their workforce reductions. They told us they are down to approximately 8,000 employees from 14,000. They have been consolidating plants – partly due to reduced capacity requirements and partly due to lean manufacturing improvements. They recently sold a major portion of their Auburn property to Safeway. In addition, they are consolidating operations out of Harbour Pointe (near Everett) into Auburn and Everett.
At our request, the tour highlighted their technology for developing custom ‘right sized’ equipment and machinery. Boeing’s first chaku-chaku line went into operation in early 1999, but faced significant management resistance. Since then Boeing has had a clear, but unpublished, intention to get out of the fabrication business and outsource it. The Fabrication Division has seized the crisis. Everyone we spoke to is very clear that they must compete against a world-wide supply base to stay in business. They want to be the “preferred supplier” for the parts they make. The Fabrication Division no longer regard their existence as a given.
Their response has been to attack capital expense.
The technology is most widely deployed in their Integrated Aerostructures operation. This is where the original chaku-chaku line was developed. That line is still in operation, along side a second generation set of equipment.
Throughout the tour I observed that they have a technology base – a consistent approach for designing and developing this equipment. But this base is not an anchor. Rather, it gives them a platform from which to improve. Each generation or project clearly adds features and sophistication (though not complexity). In all cases they are focused on single-piece takt time production with minimum capital, minimum labor and maximum quality.
Although the machine shop and emergent manufacturing are not as far along, they have boosted the level of effort in those areas by shifting people from the Integrated Aerostructures moonshine teams into those operations. The solutions we saw in those facilities were no less innovative, they simply did not have the breadth of implementation yet.
We also saw early examples of ‘bus routes’ for drop-off and pick-up of work in process from point to point, visual scheduling and pacing boards.
On the down side, their orders are still ERP / MRP generated, and they have yet to integrate their internal supply chains with pull. In my opinion this will be a difficult challenge as it requires a breakdown of traditional organizational boundaries. While they are deploying innovative production technology, those areas are still islands of flow in a largely batch environment. This is even more true in the Interiors operation in Everett (which I visited this Fall) where one-piece-flow fabrication cells are loading carts of parts that feed batch assembly operations a few feet away.
The obvious (to me) end-game would be to develop right-sized processing and finishing operations that allow detail fabrication to be exported from the Fabrication Division in Auburn to the line side at the assembly plants in Renton and Everett. Again – whether they do this or not will depend on whether Fabrication Division shift their emphasis from being a parts supplier to being a technology supplier, and overcome a reluctance to take on processes that affect metallurgical characteristics such as aging or heat treating.
Just to be clear, I did not cite this report from memory 20+ years later, I copied and pasted from the report that I actually submitted. This was my reflection at the time.
To put it simply, Boeing was on the verge of the breakthrough. They knew what to do, they knew how to do it. The approach was diffusing beyond a few staff specialists. There was a sense of purpose.
But all of this was 2002. The pivot to financially driven management had been underway for three years by that point.
The bit that is lost here is that all of these efforts were focused on improving RONA – Return on Net Assets. In Renton they were working on improving the return to get more value out of the assets that were already in place rather than continuing to add more. In Auburn they were working to develop equipment that was cheap and scalable that was just as (or more) capable as the large, expensive, automated equipment it was replacing. Less capital, more flexibility, linear scalability, little or no depreciation costs booked.
But from corporate HQ, the Jack Welch protégés that were now running the company had a quicker way to get to that RONA number: Attack the denominator: slash assets. To that end they were working to outsource large swaths of production, especially capital intensive parts like fabrication and airframe assembly; as well as a large portion of the design process itself.
By 2003 I had left the Puget Sound area for a few years and the only information I had about things happening inside Boeing at that point would be from reports in the press. The 787 program had run years behind schedule and billions over budget. The 767 Tanker program for the Air Force had been through a series of scandals, and then persistent overruns and quality issues.
Years later I joined another group touring the 737 “moving” line. By this point, though, the line was not actually moving. The tugs were just used to pull the stationary planes to the next position. We were told they would start moving the line again, “once we have solved enough problems.” The thinking had reverted – we have to solve the problems before we try, rather than trying to surface the problems we have to solve to make it work.
Fear had re-entered the equation. It was becoming palpable even to me as, now, an outsider just visiting.
Then in late 2018 and early 2019 two 737 Max planes crashed within five months of each other, for the same reason, with the loss of 346 lives.
Up to that point the cost of managing for “Shareholder Value” had been tremendous, but limited to damaging Boeing’s reputation and finances, as well as the morale in its workforce. Now people had died.
The rest of the story, honestly, remains to be told.
Boeing is at another turning point.
All of Boeing’s CEOs since the resignation of Phil Condit, have been Jack Welch protégés. Welch’s legacy at G.E. was, ultimately, to destroy the company. As I am writing this G.E. has finally completed the breakup into major divisions. Their current CEO, Larry Culp has, at least from what I have heard from people working there, repudiated the Welch era and is focusing on building a culture of teamwork.
If Boeing’s board can find the courage to admit that the results of last quarter decade have been the direct and predictable (and replicable in other companies) outcome of the way the company has been led and managed then maybe, just maybe, they have enough airspeed and altitude to recover from a flat spin.
When former Airbus executives are chiming in about what Boeing must do, it might be time to think a little harder than doubling down on what they have been doing.
They almost did it.
Thanks for this history Mark. It really gets to the details of what went wrong, and how much it will take to fix it
Excellent write-up, I learned much from it. I am sure I have used the video of the 737 moving production line in various training classes, as an object lesson and discussion piece. Always thought it was brilliant to literally implement pull, flow, takt and problem-solving that way. Here’s hoping the team regains the courage to commit to it again.
I know I have used the 737 Moving Line video quite a bit in the past – it is such an awesome example of setting up the production system to simply truthfully show what is actually happening vs. what should be happening. That being said, a lot of organizations don’t have the stomach for that kind of process transparency. It is a lot easier to just make abstract, vague, numeric reports every day.
Great sharing that gives very insightful look into one of the most interesting manufactory story in the last two decades.
I think this particular story has been repeated many times, but this case has a much higher profile than most.
Thank you Mark!
As always, very informative, insightful and a pleasure to read.