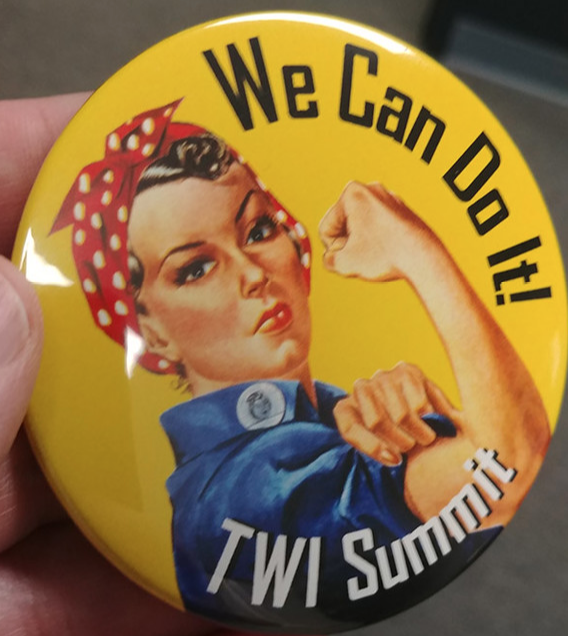
Last week (February 17-20) I attended (and presented at) the TWI and Toyota Kata summits put on by my friends at Lean Frontiers. As always, I took a few notes and I would like to share some of those notes and thoughts with you here.
To be clear, what follows are my impressions and thoughts that were sparked by some of the presentations. I am not trying to be a reporter here, just catch my own reflections.
Martha Purrier
Martha Purrier, a Director of Nursing at Virginia Mason Medical Center in Seattle, talked about “auditing standard work,” though in reality I think her process was more about auditing the outcomes of standard work. More about that in a bit.
My interpretation of the problem: Traditional “audits” are infrequent, and tend to be time consuming for those doing them because there is an attempt to make them comprehensive.
Infrequent checks are not particularly effective at preventing drift from the standard. Instead they tend to find large gaps that need to be corrected. This can easily turn into a game of “gotcha” rather than a process of building habits. What we want to do is build habits.
Habits are built in small steps, each reinforced until it is anchored.
Make it Easy: Short and Simple Checklists
Martha’s organization created short checklists of critical “Key Points” (from TWI Job Instruction) that were critical to the standard they wanted to maintain.
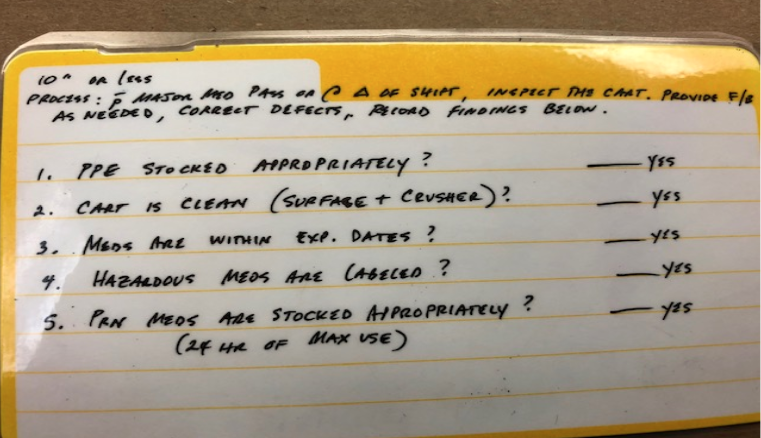
As you can see, this is a quick and simple check to see if the contents and organization of a supply cart meets the standard.
But what really caught my attention was how they are triggering the audits.
The Key: Reliable Prompt for Action
This is a pretty typical work task board. There is a row for each person or team. In this case the columns look like they represent days, but they could just as easily represent blocks of time during the day, depending on how granular you want your tracking to be. At some point these start to become a heijunka box, which serves the same purpose.
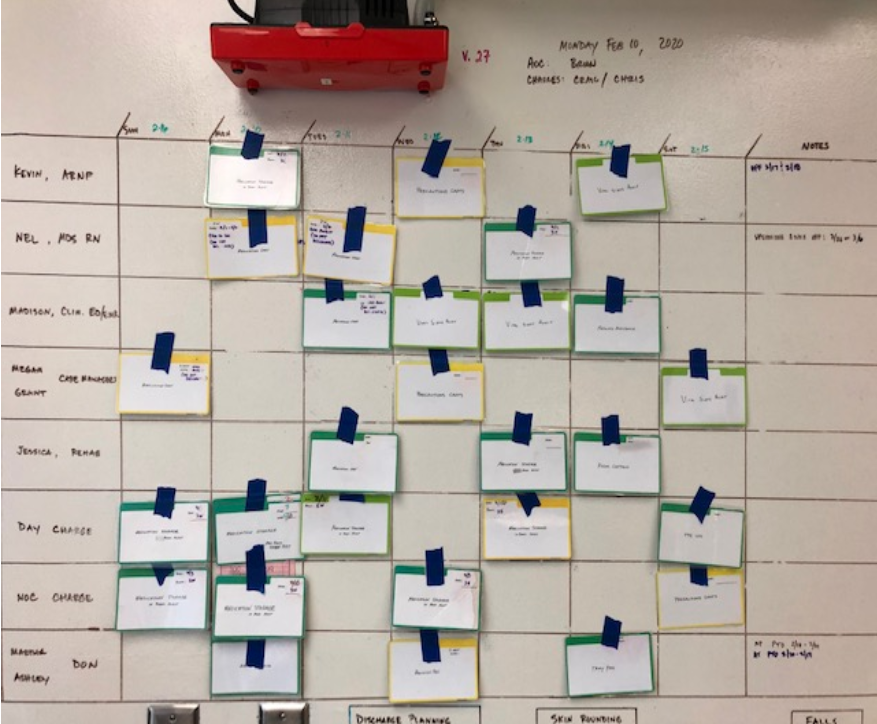
You can see the yellow bordered audit cards on there. Martha said that when a task is complete, it is moved to a “Done” column that is out of frame to the right.
Here is what is awesome about this: It gives you the ability to “pull” checks according to need.
Do you have a new process that you want multiple people to check during the course of the week? Then put the check card for that task in multiple rows at staggered times.
Do you want to go broad over a group of related checks? Then put different checks on the board.
Who should do the checks? Whoever you assign it to. Totally flexible. Do you want to trigger a self-audit? Then assign the card to the person who does the task being checked, with the expectation that they self-correct.
Do you want to bring a new supervisor up to speed quickly? Assign multiple audits to her, then assign follow-up audits to someone else.
Making it Better: Follow-up Breakdowns
If we don’t want audits to simply become lists of stuff to fix, there has to be some process of following up on why something needed correction.
Martha’s organization introduced a simple check-form that lists “Barriers to Standard Work – (check all that apply)” and provides space to list countermeasures taken.
The lists includes the usual suspects such as:
- Can’t find it
- No longer relevant
- Not enough detail
- etc.
but also some that are often unspoken even though they happen in real life:
- Lack of enthusiasm to continue or improve
- Mutiny
- Relaxed after training – drift
If a large part of the organization is pushing back on something (mutiny), then the leadership needs to dig in deep and understand why. To continue in our TWI theme, this is a great time to dig into your Job Relations process.
Standard Work vs. “Standards”
In my past post, Troubleshooting by Defining Standards, I made a distinction between defining the outcome you are trying to achieve and, among other things, the way the work must be done to accomplish that outcome.
When I think of “standard work” I am generally looking for a specification of the steps that must be performed, the order for those steps, usually the timing (when, how long) as well as the result. In other words, the standard for the work, not just the outcome or result.
To verify or audit “standard work” I have to watch the work as it is actually being performed, not simply check whether the machine was cleaned to spec.
Now, to be clear, I LOVE this simple audit process. It is an awesome way to quickly follow-up and make sure that something was done, and that the patient or customer-facing results are what we intend. It is flexible in that it can quickly and fluidly be adjusted to what we must pay attention to today.
I realize I am quibbling over words here. And every organization is free to have its own meanings for jargon terms. But when I hear the team “standard work” I am looking for the actual work flow as well as the result. YMMV.
This post got long enough that I am going to let it stand on its own. More to follow.