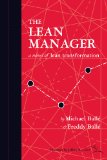
This is Part 3 of a multi-part review. Part 1 is here.
Before I get into it, I will break the rules of blogging and acknowledge a time gap here. I did finish the book shortly after I wrote part 2, in fact, I didn’t want to put it down. So now I am going back through and bringing out some key points, intermixed with some other stuff that has caught my interest lately. Anyway – back to what you came for…
Steve Spear has described the TPS as a “socio-technical system.” Put in less formidable terms, it is a system that uses the structure of the work, the work environment and the support systems (the technical part) to create an organizational culture of problem solving.
Jenkinson, Andy’s boss in the book, describes it:
“You need to organize a clear flow of problem solving, explained Jenkinson one more time. “Operators need to have a complete understanding of normal conditions, so that whenever there is a gap, they know it’s a problem. Go and see is not just for the top management, It’s for everybody. This means operators as well, in particular how they learn to see parts and see the equipment they use. How can all operators recognize they have a problem? [emphasis added]
The simple statement, and following question posed by Jenkinson sums up a great deal that is left out of lean implementations. I see it everywhere, and will be commenting on it more shortly.
We talk about “go and see” (or “genchi genbutsu“) as something leaders do. I think this is because traditional leaders aren’t naturally out in the work areas, on the shop floor, in the hangars, etc. We don’t think about the workers because they are there all of the time.
Yes, they are. But what do they see? Do they see disruptions and issues as things they are expected to somehow work around and deal with? Or do they see these things as something to call out, and fully participate in solving?
And if they do see a problem, what is the process for engaging it?
Just saying “you are empowered to fix the problem” does not make it so. When are they supposed to do it? Do they have the skills they need? How do you know? Is there a time-based process to escalate to another level if they get stuck? (Or do they just have to give up?)
And indeed, as the story in the book develops, Andy turns out to be taking a brute-force approach. He is directing staff to implement the tools and to solve problems. But in spite of nearly continuous admonitions from his boss and other experts, he is not checking how they are doing it. He has put a “get-r-done” operations manager into place, and while the guy is getting “results,” in the long haul it doesn’t work very well. Yes, they end making some improvements, but at the expense of alienating the work force.
It is only late in the story (and I won’t get into the details to avoid playing the spoiler to a pretty good plot twist) that Andy finally learns the importance of having a process that is deliberately designed to engage people.
Commentary – it is amazing to me just how much we (in the “lean community”) talk about engaging people, but never really work through the deliberate processes to do it. There are explicit processes for everything involving production, administration, etc. but somehow we expect “engaging people” to happen spontaneously just because we believe it is a good thing.
The message in this book is loud and clear. This is about leadership. The tools are important, yes, but only (in my opinion) because they are proven techniques that allow people to become engaged with the process.
But the tools alone do not require people to get engaged.
Permission to make input is necessary, but not sufficient. If you want people to be engaged, you have to deliberately engage them. Otherwise you are just asking them to become nameless cogs in “the system.”