We were down on the shop floor watching an assembly operation. The takt time was on the order of three hours. The assembler was new to the task, and the team leader periodically came by and asked if he was “doing OK.” The reply was always in the affirmative.
As the takt time wound down to under five minutes to completion, this operation was the only one not reporting “Done.”
The count down hit zero, things went red, the main line stopped, and the line stop time started ticking up.
The team leader, other assemblers, the supervisor began pitching in to assist. Between them, the job was completed in about 10 minutes, and the line restarted.
So, again, my favorite question:
What’s the problem?
Lets try breaking it down to four key questions.
- “What should be happening?”
- “What is actually happening?”
The above two questions define the gap.
- “Why does the gap exist?”
- “What are we doing about it?”
These questions simply re-frame PDCA, but without so much abstraction.
So, in this situation:
What should be happening?
Two things come to mind immediately.
- The work should be complete on time.
- As soon as you know it isn’t going to be complete on time, please tell someone so we can get you help.
For this to work, though, the team member needs a clear and unambiguous way to answer a key question of his own: Am I on track to finish on time? Ideally the answer to this question is a clear “Yes” or a clear “No,” with no ambiguity or judgment involved. (Like any “Check” it should produce a binary result.)
On an automobile line with a takt time on the order of 55 seconds, the assembler can get a good sense of this. If he loses more than three or four seconds, he isn’t going to make it. But “a good sense” isn’t good enough.
Even in this fast-moving situation, you will see visual indicators that help the team member answer this question. Take a look at this photo.
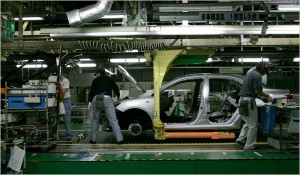
See the white hash marks along line at the bottom of the picture? Those mark off the moving line work zone into ten increments of about 5 ½ seconds. The assembler knows where he should be as he performs each task. If he is a hash mark behind, he isn’t going to finish on time. Pull the andon. We can safely say that, in this example, we have accomplished (1) and (2) above.
With longer takt times, it is much tougher for a human to have a good sense of how much time will be required to complete the remaining work. That makes it that much more critical that some kind of intermediate milestones are clearly established and linked to time.
What would be a reasonable increment for these checks? –> How far behind are you willing to let your worker get before someone else finds out? I’d say a good starting point is at the point when he can’t recover the time himself, the problem is no longer his. Following the standard work is the responsibility of the team member. Recovering to takt time is the team leader’s domain. At the very least, he is the one who pitches in and helps, or gets someone else to do so. But he can’t do this if he doesn’t know there is a problem.
So – what should be happening?
The team member must have continuous positive confirmation that he is on track to complete the work on time. With the failure of that positive confirmation, he should pull the andon and get assistance.
The team member must call for assistance (“pull the andon”) if his work falls behind the expected progress for any reason whatsoever.
What is actually happening?
In our example, the team member didn’t get help until it was too late. In fact, he verbally assured the team leader he was “OK” on a couple of occasions. The line stop was irrefutable evidence of a problem. That was a good thing. This company has a takt time, and runs to it. Think of what would have happened if they didn’t. It might take hours, or days, before this problem surfaced. (We are nowhere near the root cause yet. The line stop is just evidence of a problem, not the problem itself.)
Why does the gap exist?
It is a hell of a lot harder to answer this question than the other two. In this case, you are going to have to peel back a lot of layers before you get to the actual, systemic, root cause. But in the immediate sense, with a takt time bordering on three hours, there is really no realistic way a worker can judge if he has fallen too far behind to catch up. The fact that, in this case, the assembler was still learning the job, and that just compounds the situation.
From casual observation – when the team leader visited, he asked if things were OK and accepted the reply – I would start to investigate whether the team leader had a good sense himself of where the work should be at his regular check points… if he has regular check points at all.
But all of this is speculation, because after 10 minutes of watching the initial response to the line stop, our little group had moved on. I am mentioning these things as possibilities because you likely have the same issues in your shop. (And if you don’t have a rigorous sense of takt time, it is equally likely you don’t know about those issues even at the level we saw here. At least THIS company can see the evidence of the problem. That is a credit to their visual controls.)
What are we going to do about it?
Obviously there are a couple of immediate things that can be addressed to at least contain the problem. (That is, convert a hard line stop into multiple andon calls so the actual problems are seen earlier.)
I would want to establish a regular routine for the team leader’s checks. His leader standard work. At regular intervals, he should be checking progress of the work. How often? How far behind do you want the assembly to get before you are certain someone finds out about the problem? In this case, even every 20 minutes is less rigorous than the hash marks on the auto assembly line. But it would be a start.
So we have the team leader coming by every 20 minutes.
But he can’t just ask “How is it going?” We clearly saw that didn’t work. It isn’t that the assembler lied to him, it is that the assembler didn’t know because there was no standard.
What work should be complete 20 minutes into the work cycle? At 40 minutes? At 60? What verifiable facts can the team leader check by observation? There are a lot of ways to do this, most of them very simple and non-intrusive. Think it through.
But wait – now the team leader himself has standard work. What cues him to do it? Is he supposed to notice that 20 minutes has elapsed? In this case, the company already has a pretty sophisticated andon and sound system. It would be a pretty simple matter to put in an audible signal that told the team leader to make his checks. But, again, that is just one solution. I can think of a couple of others. Can you?
What is the team leader checking for? This is a critical question.
Think about it.
What was the original answer to “What should be happening?” (which is “the standard”)
We said:
- The work should be complete on time.
- As soon as you know it isn’t going to be complete on time, please tell someone so we can get you help.
We want the assembler himself to be checking #1.
So why do we have the team leader check?
So he can verify that the assembler is pulling the andon when he should. This is important because it is human nature not to ask for help until it is too late. This isn’t limited to factory floors. How many cardiac patients die because they ignored the warning symptoms for fear that it isn’t serious enough to get help?
It isn’t enough to ask the team member to call for help. You have to expect it, encourage it and require it.
Interestingly enough, as I was writing this post, John Shook posted his story about converting the culture at NUMMI.
A cornerstone of Respect for People is the conviction that all employees have the right to be successful every time they do their job. Part of doing their job is finding problems and making improvements. If we as management want people to be successful, to find problems, and make improvements, we have the obligation to provide the means to do so.
But, some of our GM colleagues questioned the wisdom of trying to install andon at NUMMI. “You intend to give these workers the right to stop the line?” they asked. Toyota’s answer: “No, we intend to give them the obligation to stop whenever they find a problem.” [emphasis added]
What was the problem in our example? We don’t know yet. We certainly can’t start looking for causes.
But the evidence of a problem was that the team member could not complete the work in the time expected. That is, he was not successful doing the job. And the line stopped because the support system failed to pick up the fact that he was falling behind until it was too late to recover.
It really does come down to respect for people.