Key Actions vs. Key (Performance) Indicators
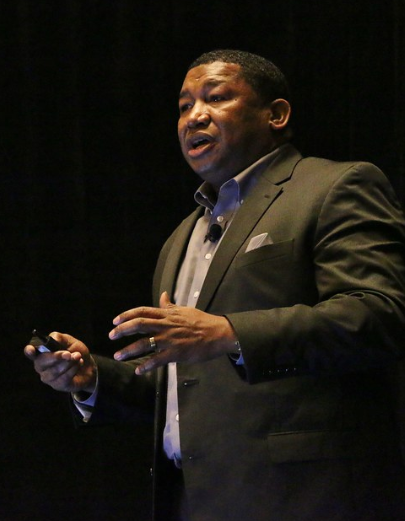
Another concept Billy brought out in his presentation was the difference between what he calls “Key Actions” (KA) and “Key Indicators” (KI) – often called Key Performance Indicators (KPI).
He actually introduced me (and a couple of other attendees) to the concept the previous evening. (Did I mention that a lot of the rich discussion took place in the lobby bar?)
We use the concept in Toyota Kata, we call them the “process metric” and the “performance metric” but I think Billy’s explanation offers more clarity than I have been able to pull off in the past.
He also ties it back into “what we must practice” to get the outcome we want.
In short, I look at the outcomes (the performance) I want, then ask “What actions, if they were carried out consistently, would give me this performance?” Those are the things that must be tracked, improved, and practiced.
I kind of addressed this concept a few years ago in Delivering the Patient Satisfaction Experience. But I’d like to focus in a little better.
Continuing on the health care theme, a key performance indicator is “hospital acquired infections” – getting sick in the hospital. Everyone agrees that this metric should be as low as possible, ideally zero.
But just tracking the “hospital acquired infections” isn’t going to nudge the needle much. There may be periods when there are improvements if there is emphasis, but year on year these things tend to be frustratingly steady over the long run.
If I ask “What behaviors, what actions, should we take to diminish opportunities for these infections?” then one thing pops right up on top: Anyone interacting with a patient must wash (or sanitize) their hands before doing so. Every. Single. Time. That action alone would have a dramatic and measurable impact.
It is so important that some systems have automated tracking to ensure compliance with this simple rule. (It is amazing to me that, in general, some of the worst offenders are physicians, but that is a rant for another day.)
Key Action: Wash your hands. Key Indicator: Hospital Acquired Infections.
OK – what about industry?
“Our machine downtime is too high. We need to improve our availability.” Key Indicator, but not directly actionable. What actions, if we take them consistently, do we believe are critical to reliable equipment?
Now we can track those. What are the critical-to-reliability things that must be checked every shift? Are they checked? How do you know? Do you track misses?
How about your preventative maintenance schedule?
Is the machine in configuration? Or are there improvised repairs in place? Why?
These are behaviors, actions, that relate directly to the availability of the equipment.
Together, they form a hypothesis: “If we carry out these actions (and know we did), then we predict this KPI will improve.” For this to work, though, we have to test whether or not the actions were carried out AND test whether or not the KPI needle moves over time.
One thing I would add: Focus on what people should do. Not so much on things they should not do. It is a lot easier to get a new habit into place than it is to stamp out an existing one. Working to replace an undesired action with a desired action is a lot easier as well.
The things that keep people from carrying out the Key Actions are obstacles. Now we can engage the Improvement Kata process and get to work.
TWI comes into play as well. “Are we carrying out the actions as we should?” It is all to easy to tell someone to do something and assume they know how, or assume that the way they do it is the way you have in mind. Trust, then verify.