The default Starter Kata for “Grasp the Current Condition” places heavy emphasis on takt time and variation in timing of a regular process. However a lot of processes, both within manufacturing as well as in other domains such as health care, don’t seem to have any kind of regular heartbeat.
As Steve Medland pointed out at KataCon, this can present a struggle for a novice learner, as well as for a lot of coaches.
Before we get into ways to deal with this, I want to level set on what takt time is, and what it does for us.
Why Takt Time?
From an industrial engineering standpoint, takt time is an expression of how much capacity you need.
The traditional way to calculate takt time is to divide the total time available by the output required in that time. This gives us a “time per unit of output” that we have to achieve if we are going to get everything done. In other words, takt time is the required rate of production.
The whole goal of an ideal “Just-in-Time” system is that we have only the capacity required to meet the demand. If the system is even able to run faster than the takt time, we have excess capacity. Excess capacity = extra cost, and “overproduction” is a symptom of having excess capacity. Note that this is the “ideal” – it isn’t anything we can realistically achieve. The concept gives us a direction to strive toward.
Also Note: Determining how much capacity you need has absolutely nothing to do with how much capacity you have.
OK, that answered the question “What is takt time?” but not the question I posed: “Why takt time?” After all, I could just as easily say I need the capacity to product 96 units per day. But that doesn’t answer the question, “How fast do I need to go?” And that is what takt time gives us.
Think of it this way. If I need to make 96 units during the course of an 8 hour day, then I need to have made 48 units in four hours.
To make 48 units in four hours, I need to make 24 units in 2 hours. Which means 12 units in 1 hour. 6 units in 30 minutes. 3 units in 15 minutes. One unit every 5 minutes. And that is my takt time. (This is an oversimplification since I did not subtract break times to make the math easier to make the point.)
Thinking of it this way gives the people doing the work a quick way to know, very quickly, if they are ahead or behind. They can ask, “How long did this unit take?” and compare that with, “How long did we have?”
A Point of Comparison
Which brings us to the “Why.”
If I measure the time between units output at the end of the line, I can compare the actual time interval (the cycle time) with the required time interval (the takt time).
- If we need to complete a unit every five minutes (takt time), AND
- We know that our process can do that when there are NO problems, THEN
- We can see very quickly if there IS a problem. We have to attack a source of variation and work on stability.
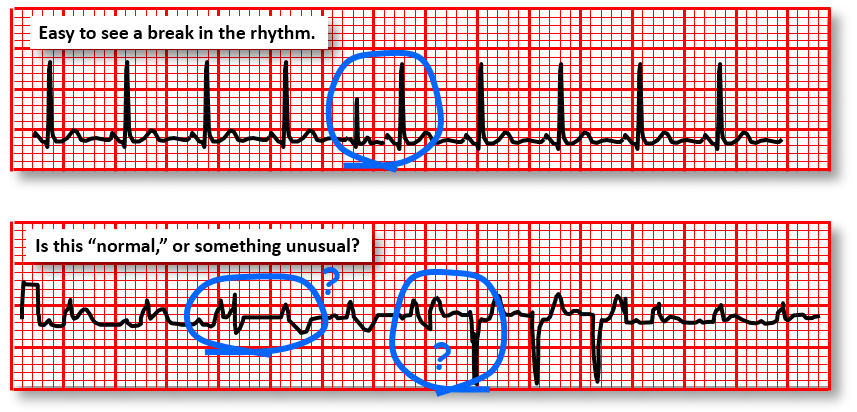
On the other hand,
- If we need to complete a unit every five minutes (takt time), and
- We know that our process is not capable of doing so even when running smoothly, then
- We know we have to change the entire system to make rate.
Distinguishing between these two conditions is the main benefit of building a cycle time run chart (step 3 in the Starter Kata of Grasp the Current Condition.) That is a topic for another post, or just get a copy of the Toyota Kata Practice Guide ;).
The issue comes when people don’t see a steady rate of demand.
Sometimes they generally know how much time is in the day, but they see demand fluctuating all over the place.
This is true in manufacturing work as well as other cases, such as engineering work, software development, and a lot of cases in health care. The time to complete one “unit of work” varies, so it is hard to see any kind of cadence to the output even if the work is steady.
Key Question: Are you ahead or behind?
And how can you tell?
Regardless of all of the variation, though, we still want to know the answer to questions such as “Are we on track to get everything done today?” or “Has my load exceeded my capacity?” or “Is the backlog increasing, decreasing, or holding steady?” unless we are simply relying on luck. Asking and answering these questions is the purpose of many of the “lean tools” – including takt time.
When to Bring it Up
Everything above, though, is information for the coach to keep in mind. What a lot of us (myself included) do all too often is take beginners into advanced application way too fast. We forget what it is like to be overwhelmed with just getting through the day, and the limits that places on anyone for taking in new concepts.
I bring it up for the coach because I think the chances of the learner discovering it on their own are significantly lower (perhaps close to zero) if the coach is starting in the same place.
If you are getting pushback on the concept, it might be time to back off a bit and give your learner some space.
Steve Medland had a mini (5 minute) presentation at KataCon 2020 that briefly addressed some of his experience with this situation.
He pointed out that the default worksheet templates for Grasp the Current Condition and Establishing a Target Condition emphasize process timing and cadence pretty heavily.
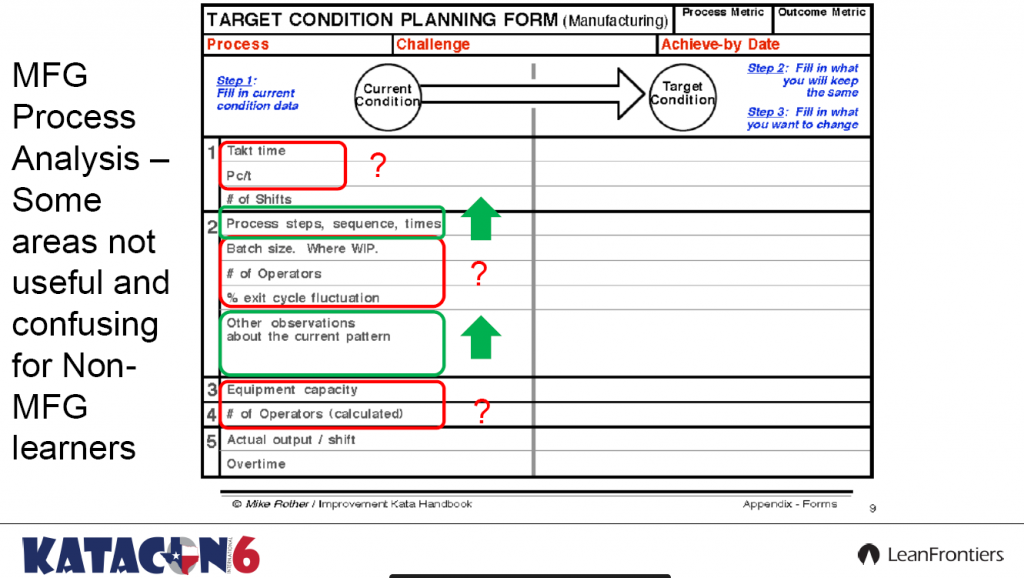
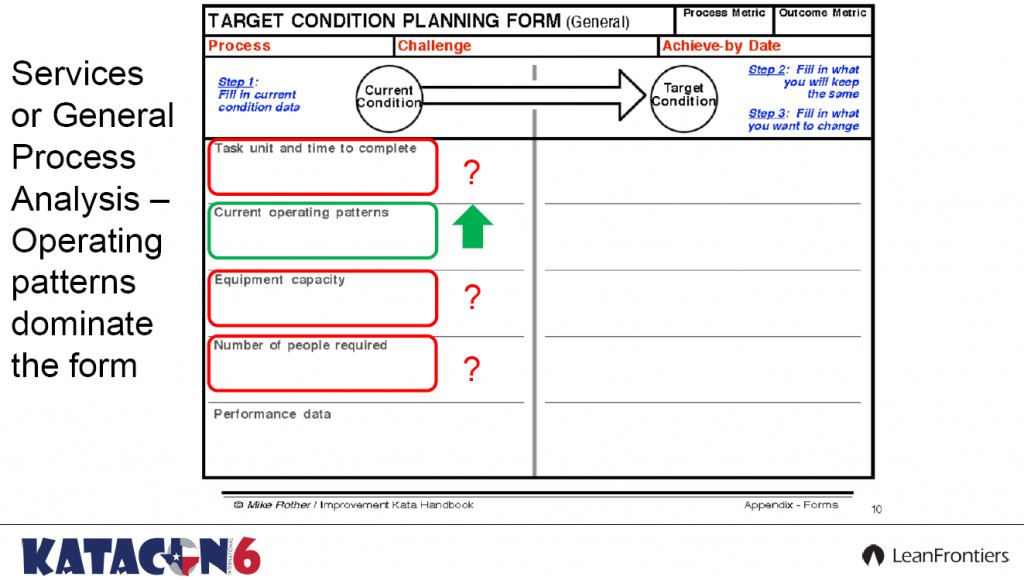
And the alternative is a blank template:
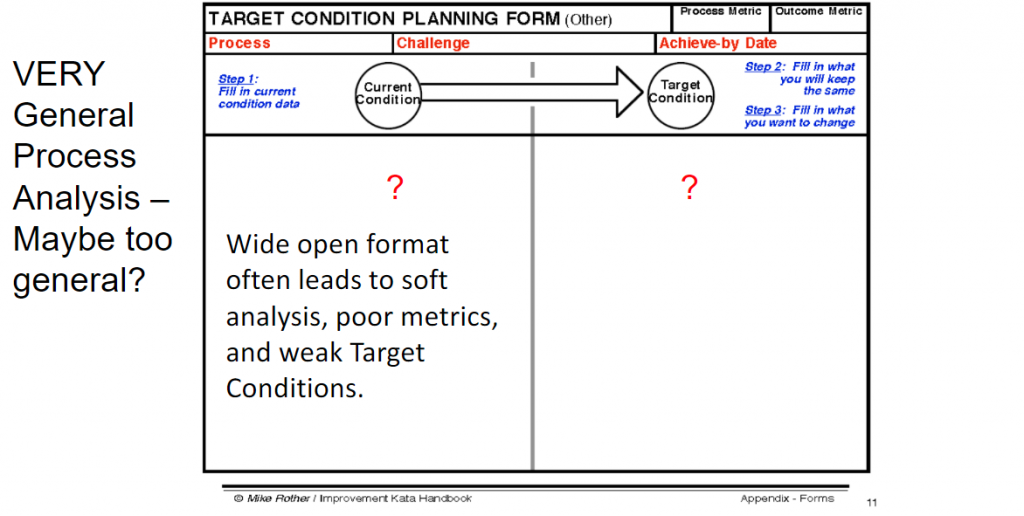
Steve makes a good case that there ought to be something that provides a more general structure without removing all structure. I agree – as a coach, structure is one of the things you are bringing to the table. Any learner, at any level of expertise, is more deeply embroiled in the process itself than in the process of improving the process. Having some structure really helps.
The key is to adjust the structure to fit the situation.
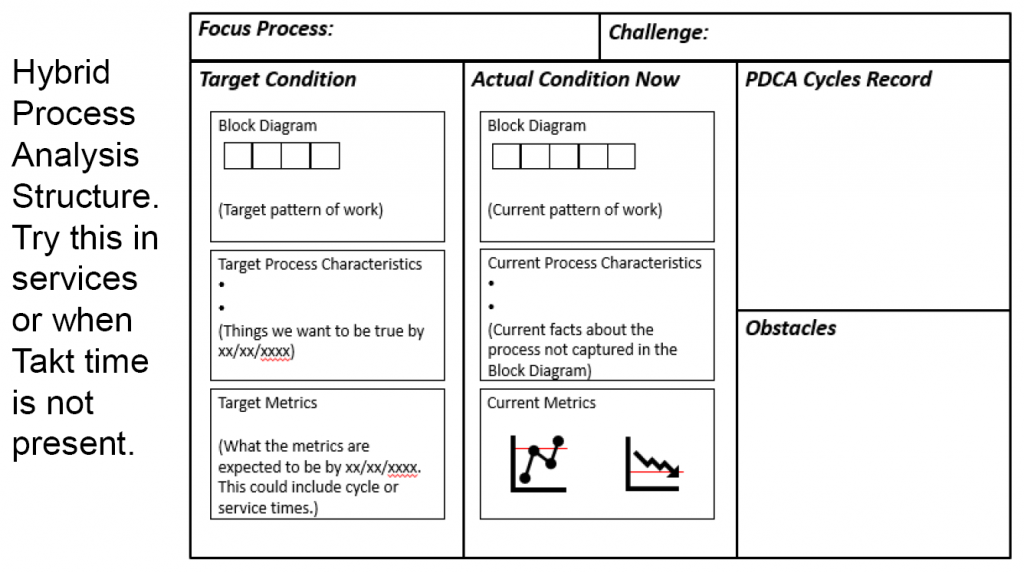
With beginners, the concept of takt time can be distracting, even paralyzing. Even more so if we use alien jargon like “takt time.”*
Using a hybrid structure like Steve proposes can get the learner moving into process analysis without getting wrapped up on terminology, or struggling with something she sincerely believes has nothing resembling a cadence.
Then, when the opportunity arises, the coach can still gently, but persistently, ask “How often does this need to be done?” and “How do we know if we are ahead or behind?”
Often the resistance is less about knowing there is some kind of schedule, and more about just being overwhelmed by all of the chaos that prevents any kind of stability.
Steve and I agree that timing is important. And I agree that it is important enough that it might be best to hold off on introducing it as a concept so we don’t create resistance unnecessarily.
But please don’t completely throw away measuring time just because it is hard. In fact, the harder it is, the more important it likely is. When it is easy to determine takt time, we likely already have an idea how long things are taking. The less appropriate takt time seems, the more critical it becomes to dig deep into where the time is going.
*Believe it or not, Godwin’s Law can even be applied to “takt time” if you research your history enough.
Your explanation is very helpful. I want to confirm that you can apply this concept to engineering work. Yes… each project can be massively different in scale. But in one company, we knew that in general every drawing (think standard blue print sheet – Metric A0 / ANSI E – with a normal detail density, meaning it could be read on a job site when printed) took 40 hours of production time (research, design, coordination, drafting, revisions). So we could actually estimate a project by setting out the list of drawings we required. And then we could tell easily whether we were ahead or behind based on how many hours we had spent and how many drawings were complete (or partially complete). It was a rough estimate – but it worked for project management purposes. We could have refined it if we had tried to use it to actually improve the process, rather than just monitor it. To bring it back to your post, although the jobs varied in complexity enormously (some jobs had 20 drawings – some 100+), there were repeatable chunks of work (activity) that took a predictable amount of time.