After yesterday’s post about trucks crashing into the famous 11foot8 bridge and mistake proofing, I got the feeling I should drive home my key point that the problem isn’t with the driver, it is with the environment.
As of this writing, Jürgen has recorded 154 crashes of overheight vehicles into the bridge.
And I’ll put even money that if all of the data were known, this process would pass any test for statistical control and we are getting what we should expect from a stable system. It might not be what we want, but it is what we should expect. (All images are copyright Jürgen Henn, 11foot8.com)

























So addressing the individual incidents probably isn’t a solution. In any case, it is unlikely that any driver will repeat the mistake.* For the TWI folks – this isn’t really a Job Relations type of problem. It might feel like it is, but it isn’t.
In the Factory
I was working with a company with a similar problem. Their inspectors kept missing defects. The response was often to say “I don’t see how she could have missed that!” and even write them up for failure to do something that wasn’t particularly well specified.
But the fact on the ground was, like the bridge, the misses weren’t confined to any particular individuals, any particular shift, any particular anything. People missed things all of the time because the expectations greatly exceeded the limitations of what humans can do for 12 hours (or even one hour). It isn’t an inspection problem. (The reliance on inspection vs. upstream controls is another topic for another day.)
People Work Within a System
It is all too easy to fall into the “bad apple” fallacy and seek out someone who was negligent. It feels good, like we did something about the problem. But the problem will happen again, with someone else. Then I hear frustrated managers start to make disparaging comments about their entire workforce that “doesn’t care” about quality.
I challenged a quality manager to do that inspection job for two hours – not even a complete shift – under the watchful eye of the inspector whose job he was trying to do. Funny – he was a lot slower to assign blame after that experience. He couldn’t keep up.
Deming was pretty clear about the ineffectiveness of exhortation as a way to get better performance. “Be more careful!” might well work for one individual for a short time. “Making an example of someone” might well work for a group for a short time. But there are norms, and the system will return to those norms very quickly. There are simple limits to what humans can focus on and for how long.
The Bridge is a Metaphor
To be clear, the bridge represents a working system, but it is different than what we would find in a company. This is public infrastructure, and the truck drivers that get featured on the videos are not part of a single organization.
This means that you have more control than the city engineers in Durham do. You can establish procedures, ask questions, train people, have them practice, alert them to the Gregson Street Bridge on their route. You can make sure your navigation system routes your trucks around the low bridges. You can support your people so they are less likely to even end up in the situation. All of these are system changes – and that is what it will take to change the outcome.
Change the System: Raising the Bridge
In late 2019 the city of Durham, in coordination with the railroad who owns the bridge, did actually raise the bridge by 8 inches. It is now 11 feet 16 inches (3.76m).
And that is a legitimate approach. Rather than trying to create infallible humans, what can we do to make the system less vulnerable to fallible humans.
While that likely reduced the number of trucks that hit the bridge…
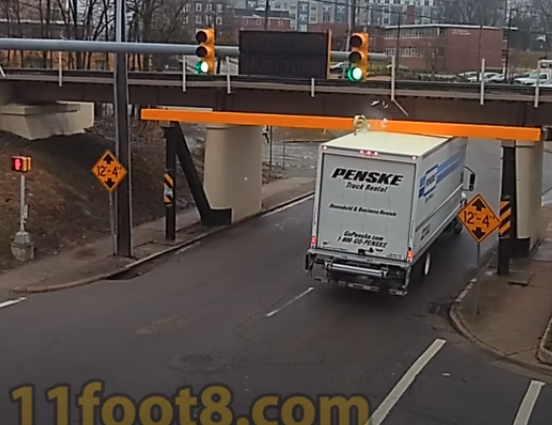
*Caveat: There is one video where a truck seems to avoid the bridge, then circle back around and hit it. And another video where a truck that hit this bridge then proceeded to run into another low bridge with the damaged truck.
My first thought is the message board, “Overheight Must Turn” sounds like a general warning. “Must Turn” is unnecessary. If the driver realizes his truck is too tall, of course he/she will turn.
How about, “Stop NOW! Your Truck Is Too Tall For This Bridge!” with flashing red lights. Or, “Stop! Your Truck Won’t Fit Under This Bridge!”
David –
Good point. The warning doesn’t come across as that urgent.
Seems like a hanging bumper prior to going under the bridge with sign on it could alert driver if too low?
I agree with David. I believe a sign that flashes and or says “Stop NOW! Your Truck Is Too Tall For This Bridge!” will be a great solution for this type of problem. Most companies know about the problems with low bridges and can redirect most routes accordingly but people who may not regularly drive trucks and are driving them like uhauls may not know any better. With technology being so easily accessible I think a sign that has sensors to read each truck driving under will be the best and easiest solution for this problem. They should put a sign like this by storrow drive in boston!
SPECULATING – GPS directions that a driver is blindly following probably contribute, as the GPS app has no idea of the vehicle it is guiding.
But, as I mentioned above, I would prefer that people see the scenario as a metaphor for the human nature in your own organization vs. trying to solve the low bridge problem.
This is an interesting point that you make about managers having realistic notions about the jobs their employees can complete with the restrictions imposed upon them. Often times the preset process can be traced back to the problem where these managers have no clue of the difficulties source, especially in this case where the results are trucks crashing into bridges. This prompts us to ask what can we do as managers to fix this and save the company money? Would short scheduled meetings help where all party’s involved meet to discuss possible scenarios and their solutions help? Or will rerouting the trucks around low bridges solve their issues and will this create a new issue for deliveries like longer lead times?
Think of the low bridge scenario as a metaphor for issues that might come up in your own organization rather than a specific problem to be solved.
Remembering the bridge as a metaphor seems like a great way to analyze issues in a work place. There is never an easy solution to a core problem. Punishing an employee may seem like a quick solution but the problem will repeat over and over again. The truck driver seems like they are inexperienced for not noticing the height of the bridge. However, the real issue isn’t the driver but the environment they are in. If there was a large red blinking sign to warn drivers then the problem may occur less no matter how experienced the driver is.