The teacher hasn’t taught.
This article, titled “Why China is Not Ready for Lean Manufacturing” presents an account of trying to teach “lean manufacturing” in a Chinese factory. The experience is summed up in a couple of key paragraphs:
The team arrived in Dongguan and went to work giving an overview class on Lean techniques. The factory workers seemed attentive and interested in learning. The next day, the Silicon Valley Lean team gathered the people from the assembly line to begin the process of working on the quality problem. After 3 hours, the Lean team ended the session in utter frustration. No one participated. No one would identify problems on the line. No one knew how to approach gathering or analyzing data. No one volunteered.
So what happened? The training was adequate and the Lean principles and methods are sound and easily understood. Why weren’t the Chinese factory workers participating?
Why indeed?
The author’s conclusion is that Chinese worker’s culture and values conflict with the idea of collaboration and contributing ideas to improve production quality and efficiency.
But the article brought up two separate thoughts.
First, there is nothing magic about Western culture. These concepts can, and do, fall just as flat in the USA and Europe as they did in this factory. The problem in these cases has less to do with the national culture, and more to do with attempting to apply a rote approach to teaching.
Second, the result cited here was exactly the opposite of my own experience in a Chinese factory.
It took some persistence, and it took some deliberate steps to remove fear from the factory floor, but in the end we had these Chinese workers making some very innovative contributions.
This photo is an old boring mill. It was a slow old boring mill. We needed to squeeze cycle time out of the process to make the projected takt time. We showed the workers some photos of other teams’ efforts to mock-up fixtures so they could quickly try out ideas. The workers, after a few false starts, constructed what you see here, and ended up with a pretty good set of fixtures that could be loaded and unloaded quickly. After some trials, they figured out on their own that they could fit two fixtures on the platform, which allowed them to be unloading and loading one while boring on the other.
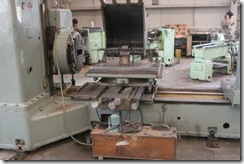
One of the machinists complained that the machine could run faster if it had a liquid cooling system. With encouragement, he designed and built a simple, but working, cooling system for the cutting tools. (The steel box in the foreground with a pump on it.) The clever part was the chip filter made from a bottle cap and a nail.
Another team was working on a welding cell. They ended up designing and fabricating more efficient fixtures than had been provided by the engineers. Then they set out to develop the most efficient way to get parts positioned, to load them quickly into the fixture, and weld up the part.
What was different?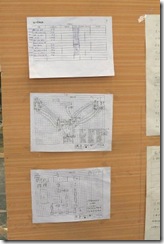
First, we didn’t do any classroom education. Not quite true. We showed them photos of really good welding fixtures that had been designed by a sister company. That took about 30 minutes. We explained what features made those fixtures good. Then we continuously encouraged them to try things so they could learn on their own. And try they did.
We didn’t ask them to go beyond mock-up. We fully expected to take their ideas, turn them over to engineers to get them finalized and drawn up, then have the fixtures fabricated. But the workers took it on their own initiative to dig through the (embarrassingly large) amount of scrap metal out back, bring in what they needed, machine parts, scrounge others, and built their fixtures in steel.
A number of ideas were things I could clearly see would not work. I knew that heat distortion from welding would make a particular fixture design difficult (impossible!) to unload after welding. I could tell them it wouldn’t work, or I could let them try it on their own. I chose the path that would engage their curiosity and let them learn through experience. They became better welders for it.
Honestly – this was a slow time while we were working out other issues with market positioning, sales, design and sourcing decisions, and most of this activity was intended to keep people busy and engaged. But what we ended up with was production-ready work cells, all built upon ideas from the workers.
So why did I tell this little story?
First, I will admit that I was pretty proud of these guys. This was a few years ago now, but it was fun blowing away everyone’s stereotypes about Chinese factories and Chinese workers.
But I wanted to make a key point.
Instead of looking for cultural reasons why “this won’t work here” we kept faith that, if the initial response was silence and non-participation, there was something that we needed to address in the way we taught, and in the environment we were creating.
Indeed, what the Chinese culture brings to kaizen is a centuries-old tradition of improvising with what you have to get something done. This is a great strength that can be hard to find in cultures with longer traditions of wealth.
Just as we were encouraging these workers to try things so they could learn what did work, we had to do the same thing. We didn’t give up after three hours. Eventually we managed to remove the fear and bring out the best these people had to offer.
Classroom education is actually a very poor way to teach people how to study a process, understand it and improve it. Sometimes it kind of works, but I think that is because it is marginally effective if all of the other conditions are right. Perhaps in some cultures that starting point is past the limit of what classroom education can handle. That isn’t a problem with the culture, it is revealing the inherent weakness in the approach.
There is no cookbook. There is only a clear objective, and good faith effort to keep trying until a solution is found.
Epiloge: Yes, this factory got into production. However the parent company could never get traction in this market with this product and recently made a decision to close this plant and pursue a different strategic direction. That is not a reflection at all on the people who did the work in these photos.